Shell’s Singapore complex to get digital twin
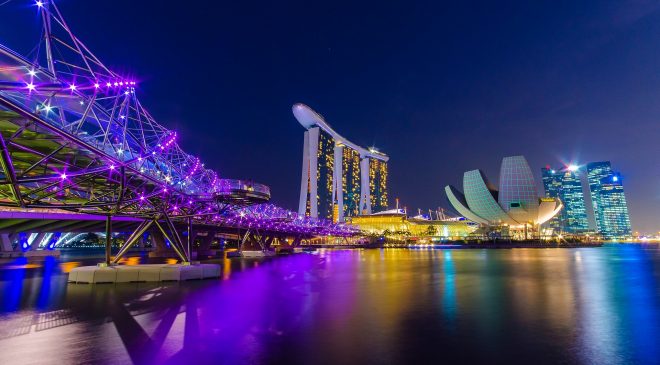
Technology will generate a complete virtual twin of the physical elements on the oil and petrochemical manufacturing site.
The Singapore Economic Development Board (EDB) has announced that energy giant Royal Dutch Shell will start a four-year pilot project to digitalise its Pulau Bukom refining complex.
The complex is an integrated oil and petrochemicals site with manufacturing facilities for fuels, lubricant base oils and specialty chemicals.
The Bukom manufacturing site has developed into one of the most important Shell production sites in the world. And is one of the the largest wholly owned Shell refinery globally in terms of crude distillation capacity (500,000 barrels per day).
Pulau is also home to a world-class Ethylene Cracker Complex (up to a million tonnes per annum) and a Butadiene Extraction Unit (155,000 tonnes per annum). The site also produces base oils, which is sent to Shell’s Tuas Lubricants Plant. Bitumen produced on Bukom, along with lubricants produced from base oils, are supplied to China and across South East Asia.
Its advanced manufacturing site technology, called Digital Twin, is expected to boost productivity, reliability and safety.
When fully implemented in 2024, the technology will generate a complete virtual twin of the physical elements on the oil and petrochemical manufacturing site.
Digital Twin will allow operators to dynamically respond to changes in conditions in facilities on the site, the company said yesterday.
EDB states Pulau Bukom was picked for the initiative as it has a strong track record in piloting path-breaking digitisation projects and a long history here.
Shell employs 1,300 people at the 59-year-old site – the company’s Asia-Pacific hub for integrated fuels and petrochemicals and home to Singapore’s first refinery.
While the new technology will improve productivity and efficiency, a Shell spokesman said, “there is currently no plan to review our manpower needs as a result of the Digital Twin”.
The company said the digitalisation of Pulau Bukom is aligned with the Singapore Government’s focus on Industry 4.0, which will see automation powered by data to perform everyday tasks.
“We are committed to making our Singapore sites on Bukom and Jurong Island globally competitive by combining human capabilities with advanced digitalisation technologies, to truly transform the ways we work,” said Hugues Bourgogne, Shell’s vice-president of manufacturing for Singapore/Philippines and general manager of the Pulau Bukom manufacturing site.
The power of the Digital Twin technology lies in its visual, data and analytics capabilities.
Complete virtual representation of the physical elements of Shell’s Pulau Bukom manufacturing site.
Able to respond dynamically to conditions based on data from more than 20 technology platforms.
Live information of plant operations can be provided to engineers via augmented reality and virtual reality, reducing the need to enter the facility.
All critical field operations at the site will be performed through tablets (above) by 2025.
Live information of plant operations can be provided to engineers via augmented reality and virtual reality, reducing the need to enter the facility.
All critical field operations at the Pulau Bukom site will be performed through tablets by 2025, Shell said.
EDB notes that since late last year, about 140 employees from various teams at the Pulau Bukom site have participated in hackathons and digital boot camps to bolster digital capabilities at the site.
All employees, including management, engineers and technicians, will be trained to operate the technology over the next two years.
Shell is committed to investing more than 6,000 training hours annually from next year to push its digital initiative here.
The Pulau Bukom site can process up to 500,000 barrels of oil a day, making it Shell’s largest petrochemical production and export centre in the Asia-Pacific region.
Shell has already implemented digitalisation solutions such as drones, 3D printing and augmented reality at manufacturing plants here, including Shell Jurong Island.
Digitalisation has also changed the way construction work is done. Staff can use 4D-and 5D-based construction planning to accurately predict constraints and monitor developments, resulting in time and manpower savings.
Damian Chan, executive vice-president at the Economic Development Board, said it was encouraged Shell has taken this bold step of piloting the Digital Twin solution in Singapore, “setting a strong example of how the energy and chemicals sector can adopt technology to move towards Industry 4.0 standards”.
He said Shell’s investment in digital processes, technologies and training will help advance Singapore’s push for digital transformation.
Tags: big data, digital twin, Shell, Singapore