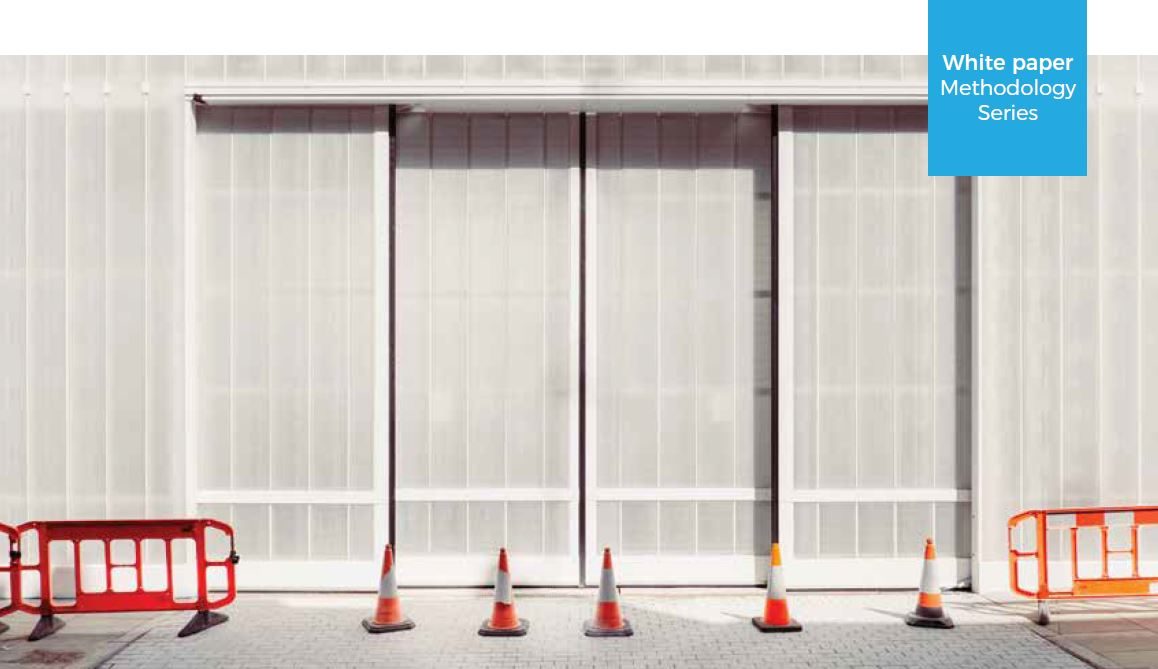
Introduction
How do you measure safety in your workplace to enhance performance and reduce employee downtime? There are several tested methods that Environmental, Health, and Safety (EHS) leaders use to reduce employee incidents and illnesses. Among the leading methods, which this white paper discusses, are Key Performance Indicators (KPIs)–or leading and lagging indicators. Leading indicators are pre-incident measurements, as opposed to lagging indicators, which are measurements collected after an incident occurs. For example, a slip and fall incident from stray construction materials is a lagging indicator because the incident has already occurred, but an inspection that notes the poor quality of the surrounding area and prevents a future slip and fall from taking place is a leading indicator. A key component of leading indicators is that they measure safety events or behaviors that precede incidents and have a predictive quality.
By measuring leading indicators including conditions, events and sequences that precede and lead up to accidents, these KPIs have value in predicting the arrival of an event and can provide the opportunity to introduce control measures to stop the event from happening.
Recently, many articles have stressed the importance of looking beyond lagging indicators, but then how can your organization learn from past incidents and track results? By combining incident measurement and training management software, your company or organization can adopt a holistic approach to reducing workplace incidents and meeting Occupational Safety and Health Administration (OSHA) standards.
Both leading and lagging indicators can be relevant to workplace safety and worth measuring. They present important aspects of an overall safety management system. We have to use all the tools available to us to create an environment that drives us to a zero-incident job site.
Selecting and Using the Right Key Performance Indicators (KPIs) for Your Organization
Attempting to track complex data analytics and results, train employees and keep your team safe on your own can be dicult tasks to handle. Leading and lagging indicators can help reduce and prevent incidents. One way EHS leaders begin using KPIs is by selecting the
appropriate sets for their organization.
Lagging Indicators
- OSHA recordable injuries
- OSHA citations
- OSHA recordable-case rate
- DART-case rate
- Fatality rate
- Worker compensation claims
- Experience modification rate
Leading Indicators
- Near misses
- Behavioral observations
- Training records
- Department safety meetings
- Employee-perception surveys
- Trainee scores on post-training quizzes
- Preventive-maintenance programs
When trying to pinpoint the indicator type essential for your organization–understand that both are essential. Leading indicators are like a car windshield, and lagging indicators are like the rearview mirror. You’ll certainly spend more time looking out the windshield to see what’s coming–with leading indicators–than looking in your rearview mirror to see where you’ve been–with lagging indicators. Look at your company and see how you can start moving forward–toward a culture of safety–rather than looking behind.
Within the leading and lagging indicator types, there are eight important characteristics that KPIs should have. Ensure that you follow this guideline when selecting the ones important for your workplace.
1. Actionable–metrics that have measurable steps
2. Achievable–setting goals that are obtainable
3. Meaningful–obtaining information for continued tracking
4. Transparent–metrics that are clearly understandable
5. Easy–to communicate effectively
6. Valid–relevant to the organization’s objectives
7. Useful–metrics that are beneficial to the organization’s safety goals
8. Timely–distributing information that is still relevant to the organization
Once you select your set of indicators and follow the necessary characteristics, it’s important to track how well they are working and be flexible if the set needs to be revised for consistent improvement.
Why Leading and Lagging Indicators Are Important: Rising OSHA Regulations & Safety Trends
Each year brings about new regulations and carries over existing regulations that companies must abide by. Thus, it’s important to stay on top of ever-evolving regulatory trends so you don’t risk non-compliance. Use the leading and lagging indicator system to help with the following key OSHA regulations and safety trends.
Overview of the Occupational Exposure to Crystalline Silica Rule
OSHA’s final rule aims to reduce the risk of lung cancer, silicosis, chronic obstructive pulmonary disease and kidney disease in America’s workers by limiting their exposure to respirable crystalline silica. The rule is comprised of two standards, one for Construction and one for General Industry and Maritime. Responsible employers have been protecting employees from the harmful substance for years, but now it’s becoming mandatory. Here are some of the rule requirements:
- Reduces the permissible exposure limit for silica to 50 micrograms per cubic meter of air
- Requires employers to: use engineering controls to limit worker exposure; provide respirators when engineering controls cannot adequately limit exposure; develop a written exposure control plan, and train workers on silica risks and how to limit exposures
- Provides medical exams to monitor highly exposed workers and gives them information
about their lung health
Overview of OSHA Improve Tracking of Workplace Injuries and Illnesses Rule
The Bureau of Labor Statistics reports more than three million workers suffer from a workplace injury or illness every year. Currently, little or no information about worker injuries and illnesses is made public or available to OSHA. With this new rule, employers are required to submit a record of the injuries and illnesses to OSHA to help them with identifying hazards and fixing problems. Here are the rule requirements:
- Establishments with 250 or more employees must *electronically submit injury and illness
information from OSHA forms 300, 300A and 301 (300 & 301 starting in 2018)
- Establishments with 20-249 employees in high-risk industries must submit information from OSHA form 300A
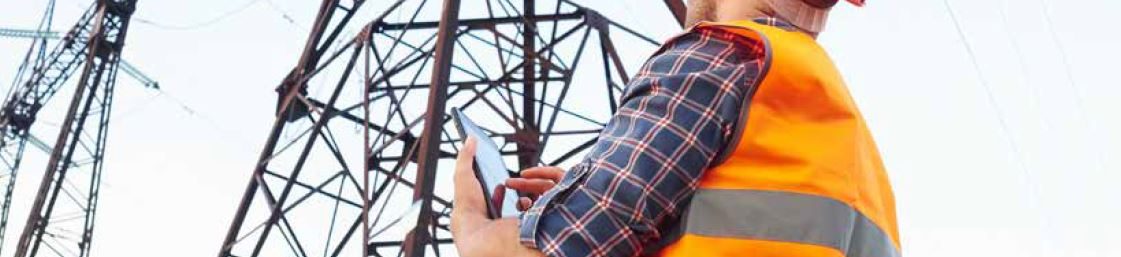
Trend #1: Dealing with Workplace Stress
The National Institute of Occupational Safety And Health emphasizes that work-related stress disorders are expected to rise as the economy continues to undergo various shifts and impacts. Therefore, companies should take steps to ensure that any current programs are robust enough to reduce the concerns associated with stress in the workplace, as well as implement any new programs that show an increased effectiveness at reducing the generation of stress.
Trend #2: Leveraging Risk Management
2017 saw a continued trend in developing internal risk management programs and systems, and 2018 into 2019 looks to be the year where many of these programs are leveraged for results across the company spectrum. In other words, sufficient time has occurred for the internal development of risk management data and effectiveness that this can now be translated directly into specific areas of the business to further reduce inherent risk development within the company.
Trend #3: Increased Reliance on Predictive Analytics
A new trend becoming prominent in 2018 is an increased reliance on predictive analytics. Many companies have been developing risk management and mitigation data and using analytics to help derive sense from this mountain of information. 2019 looks to be the year where many of these are put into practice company-wide. In addition, the trend of emphasizing the use of these predictive analytics is expected to rise as much of this information is refined even further. This should begin to show positive returns for companies that have been implementing this predictive technology as part of a risk management profile. However, there is still time to take advantage of these systems for those companies that have not implemented these types of analytics.
Trend #4: More Regulatory Changes
There are few that doubt that more regulatory and legislative changes are expected in 2018. While many differences continue to grow between national policy and those enacted on the state and local level, few can predict what the specific changes will actually be. However, what is an almost certainty is that for companies, flexibility will be necessary in order to adapt to the new policies to come.
Models and Methods for Using Leading and Lagging Indicators: A Contextual and Visual Guide
Various proven, yet antiquated and manual, methods have been used for measuring KPIs, such as those discussed in the report, A Method for Modeling of KPIs Enabling Validation of Their Properties. The authors cover two techniques workplaces use to track KPIs.
The first model integrates the following attributes for tracking performance: indicator name, type, scale, source, owner and threshold. Though, it is not easy to find all of this information so EHS experts often rely on documentation, expert knowledge and previous conceptual models.
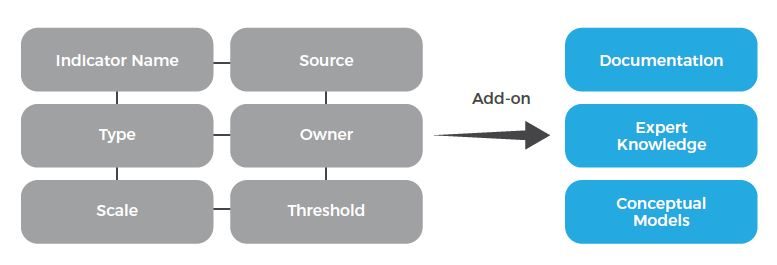
The second model used for KPI formalization is known as performance indicator expression. It is “a mathematical statement over a performance indicator evaluated to a numerical, qualitative”. In other words, a given value for a time point, for the organization, unit or agent. The authors suggest specifying the required values of performance indicators as constraints coming from goals. The relations between performance indicators are modeled using predicates.
The third model used by EHS professionals and safety teams is known as the Heinrich Pyramid–a traditional way of tracking occupational illnesses and injuries.
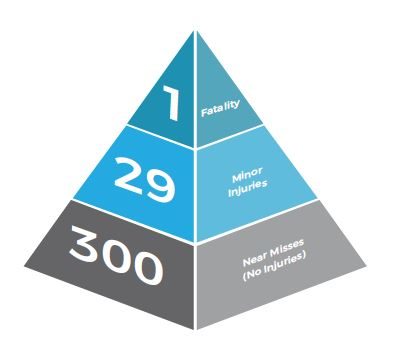
The Heinrich Pyramid (also known as the Safety Triangle) quantifies the number of reported workplace incidents into four main categories: major injuries, severe accidents, first aid cases and near misses. Employee concern reports, safety observations and at-risk observations can also be added to the base of the triangle to incorporate leading indicators into the analysis.
This is a 1-10-30-600 model. For every 1 incident reported in the major injury category, severe accidents are 10 times as likely to happen. Also, for every 1 major injury, approximately 30 first aid cases, and 600 near misses.
When companies plug their own incidents into this model or pyramid, they can see if they have the corresponding model ratio, as described above, and if they have a significant amount of major and severe incidents. The premise for this model is that the more companies focus on reducing the numbers at the bottom of the pyramid, the more likely they are to reduce major safety incidents at the top.
The pyramid is inclusive of many types of injuries and incidents, but it doesn’t assist EHS professionals with narrowing down the data to the critical cases/accidents, root causes and solutions. For example, a site could have a series of cases that stem from ergonomic-related issues and spend significant amounts of time on root cause and trend analysis instead of the cases/accident that have a high potential to result in an employee fatality or significant property damage.
Critics of the Heinrich Pyramid also claim that “adhering to it can lead to an over-emphasis on worker behavior and not enough attention on health and safety management software systems.” No matter the flaws, there is always a solution to the system. These methods are used to benefit companies’ safety success rates and business performance objectives. The methods can be adapted to any enterprise modeling approach. Companies can apply these measures of thinking into a conventional and modernized process by integrating EHS management software into their workplace as discovered in the following section.
A Gensuite Solution: Implementing Key Performance Indicators (KPIs) Into Your Workplace
To simplify and digitize the three models and methods discussed above, companies turn to compliance and management software systems such as Gensuite. Such systems enhance workplace safety performance by simplifying the tracking of leading and lagging indicators. Utilize Gensuite EHS software tailored to measure KPIs and manage training compliance. Just a few of Gensuite’s specialized features of these tools include:
- Framework for managing regulatory and program-specific training requirements.
- Validate training effectiveness through course-specific e-quizzes
- Incident investigation, root cause analysis, corrective and preventive action tracking
- Integrate with occupational health, medical and computer systems for case tracking and program visibility
What makes this important right now? Why should your business invest? Other than avoiding everyday safety violations and reoccurring workplace injuries, investing will help you meet current and upcoming OSHA regulations. Here’s a look at customizable Gensuite applications.
Incidents & Measurements
The Gensuite Incidents & Measurements application can help you address the new regulation by enabling one-click generation of a site/business OSHA 300, 300A, and 301 forms. In addition, Gensuite joins ongoing discussions with subscribers and industry groups to meet with OSHA to talk through options for direct system integrations, thus removing the need for sites to manually generate logs and input them into OSHA’s website.
Other benefits of the Gensuite Incidents & Measurements application:
- Tracking of hours worked and sites recordable rates
- Monitoring site performance on a monthly/quarterly basis through auto-generated site metric reports
- Instant system-generated email notifications upon entry/modification of incidents so site-leadership stays up-to-date
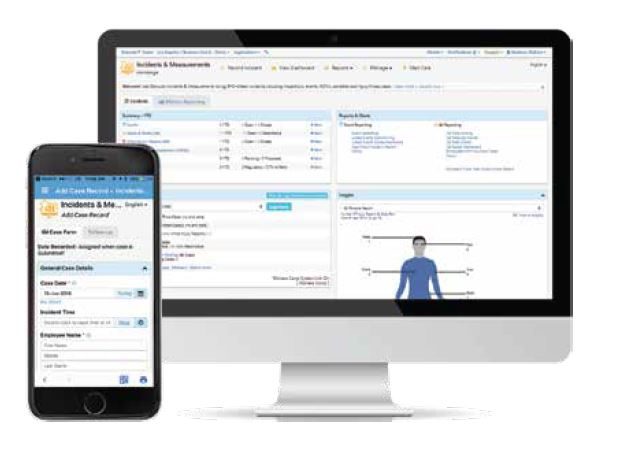
Training Compliance
The Gensuite Training Compliance suite can help you address both new OSHA regulations by keeping your employees up-to-date with OSHA’s mandatory training requirements. In addition, training employees prevent new and future injuries from occurring, so you don’t have to evaluate progress based on how many employees have been severely injured and how that number has improved. Prevent them from happening in the first place.
Other benefits of the Gensuite Training Compliance application:
- Establish a framework for managing regulatory and program-specific training requirements, alert training leaders of new and transferred employees for training needs assessment
- Integrate automatic updates from HR systems, offer multiple training instruction types to engage employees in classroom and e-learning training; integrated training calendar solution for session scheduling, provide employees with access to a diverse library of pre-loaded training content licensed from leading providers such as RedVector®, SkillSoft®, PureSafety®
- Validate training effectiveness through course-specific e-quizzes; log completions through online, bar-coding, Mobile & batch upload
- Identify qualified employees by task based on training completion status
Plan now for the program changes needed! Contact Gensuite today to know more about how we can help you meet mandatory regulations and track KPIs. Look to Key Performance Indicators so your business can avoid safety violations and injuries. Who doesn’t want the satisfaction of being a part of a workplace that has been accident and incident free for 90 days (or more)?
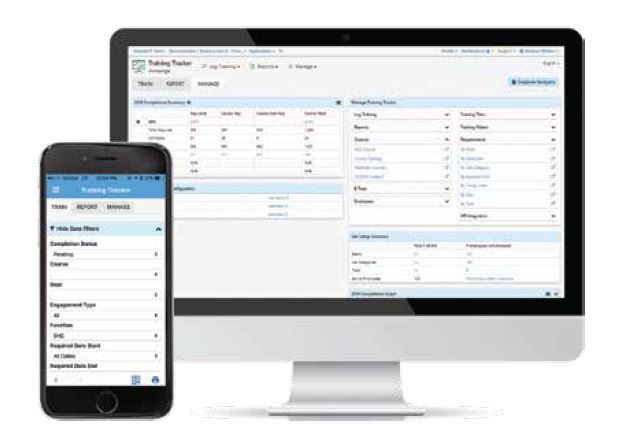
Conclusion
Now you have the tools you need to enhance your workplace safety performance. After reading this white paper, you should be able to select the right KPIs for your organization, understand the models and methods for using leading and lagging indicators and lastly integrate Gensuite software solutions into your workplace to track leading and lagging indicators. Let Gensuite be your guide to a safer workplace.
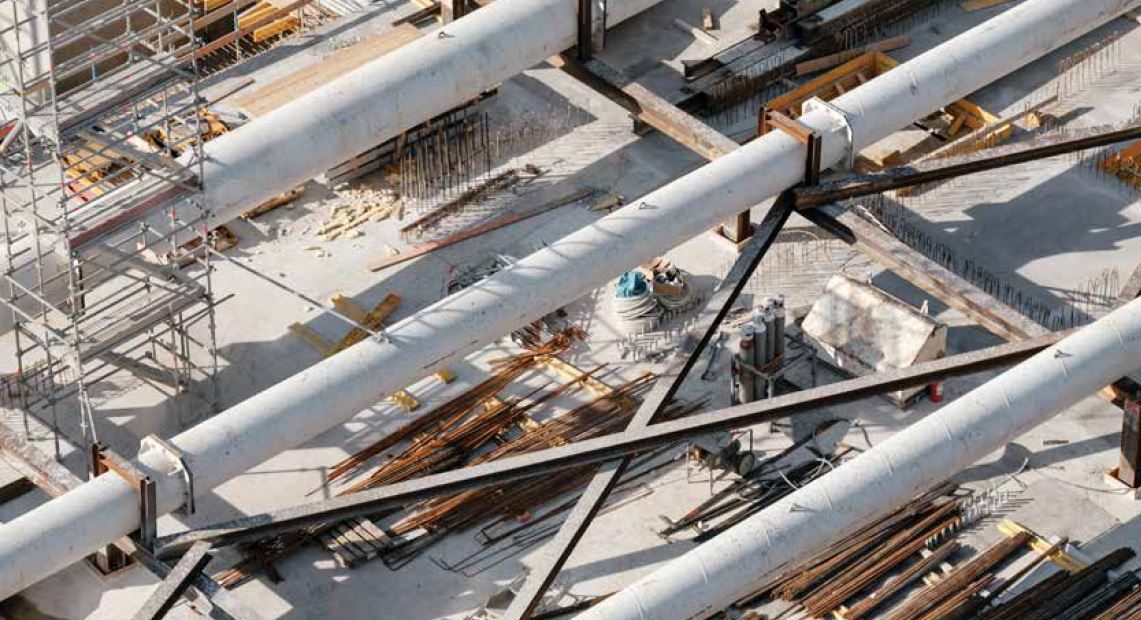
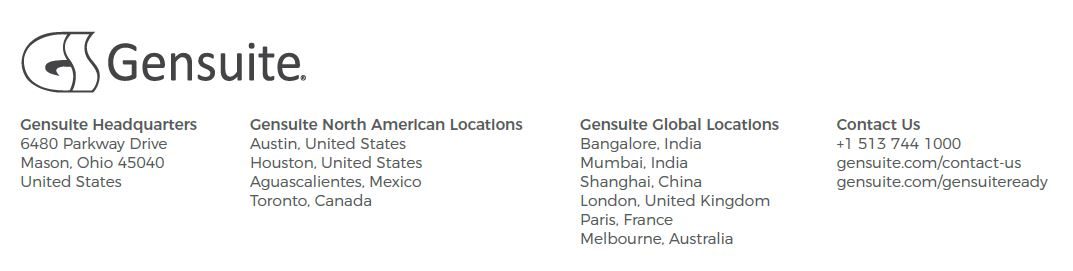